According to the Occupational Safety and Health Administration (OSHA), 80 percent of workplace accidents are caused by behaviors, and 20 percent are caused by unsafe conditions. Recognizing these dual challenges has shaped the way we hire, train, support, and verify safety on the job.
HBW views safety as an all-or-nothing issue – you’re either 100 percent all in, or you’re unsafe. It sounds a bit dramatic, but we see job site safety as a sign of respect. Respect for our workers, respect for our clients, and respect for our craft. For HBW, doing the job right means doing it safely.
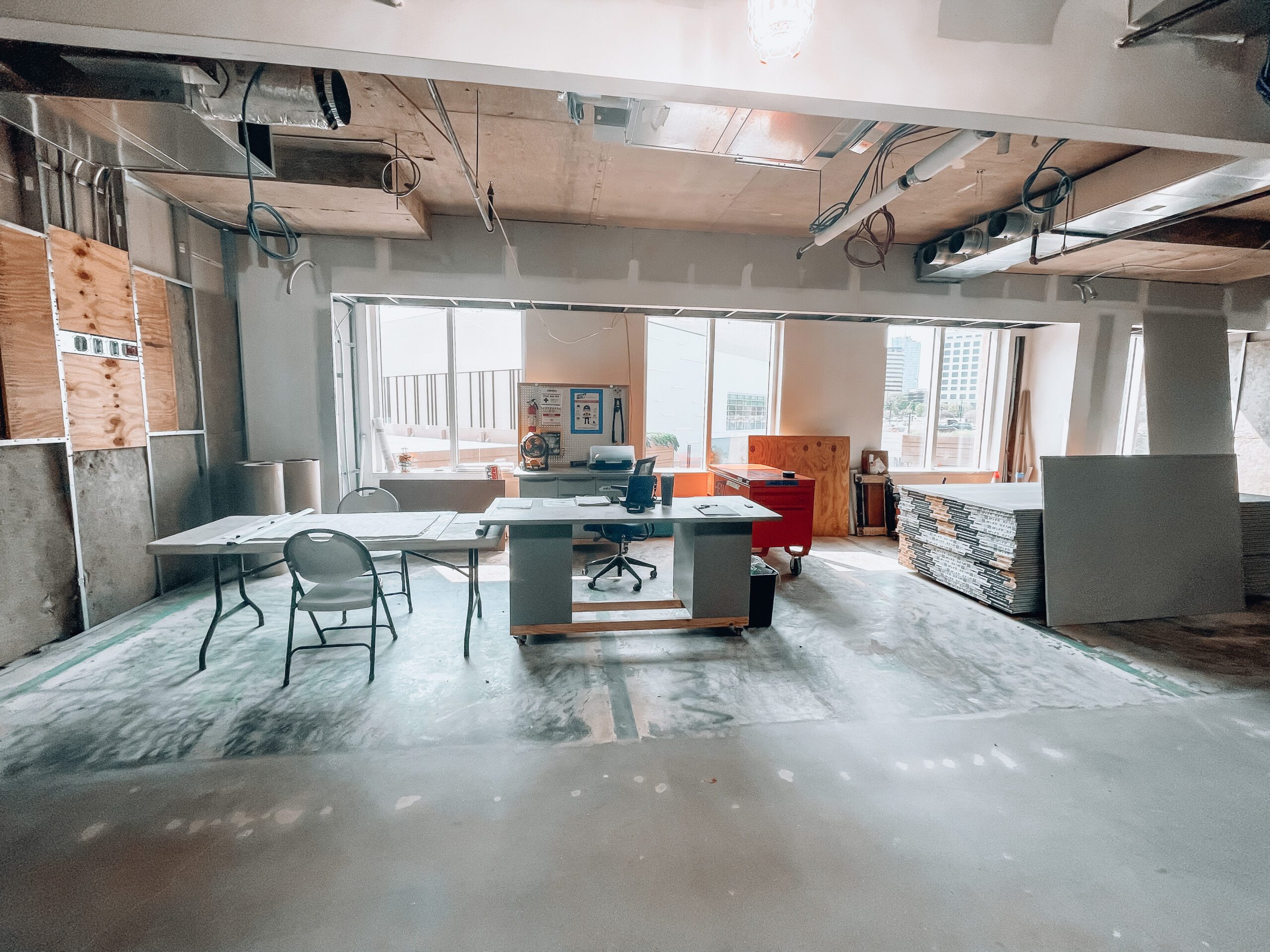
Safety, from the top down
Safety at HBW starts at the top and trickles down. We train all of our superintendents to uphold our level of construction safety. No matter their experience level, we have new superintendents shadow a senior superintendent team leader for weeks, learning our expectations for safety in every facet of the role, from following guidelines to communicating with staff. We have even created a unique trainer position to provide instruction and mentorship for those moving up in our ranks. Our investment of time and resources sets us apart from other companies in our region.
All new employees are required to go through HBW Construction’s safety orientation covering safety prevention, procedures, and response measures, setting the tone for safety awareness. Our subcontractors receive our safety manual and policies too. Our expectation is that they will arrive properly equipped to do their job with personal protective equipment (PPE) and proper tools – but we don’t leave anything to chance. Our superintendents are responsible for verifying their readiness, preparing them to enter and work on the construction site, and alerting them to any special hazards or job requirements.
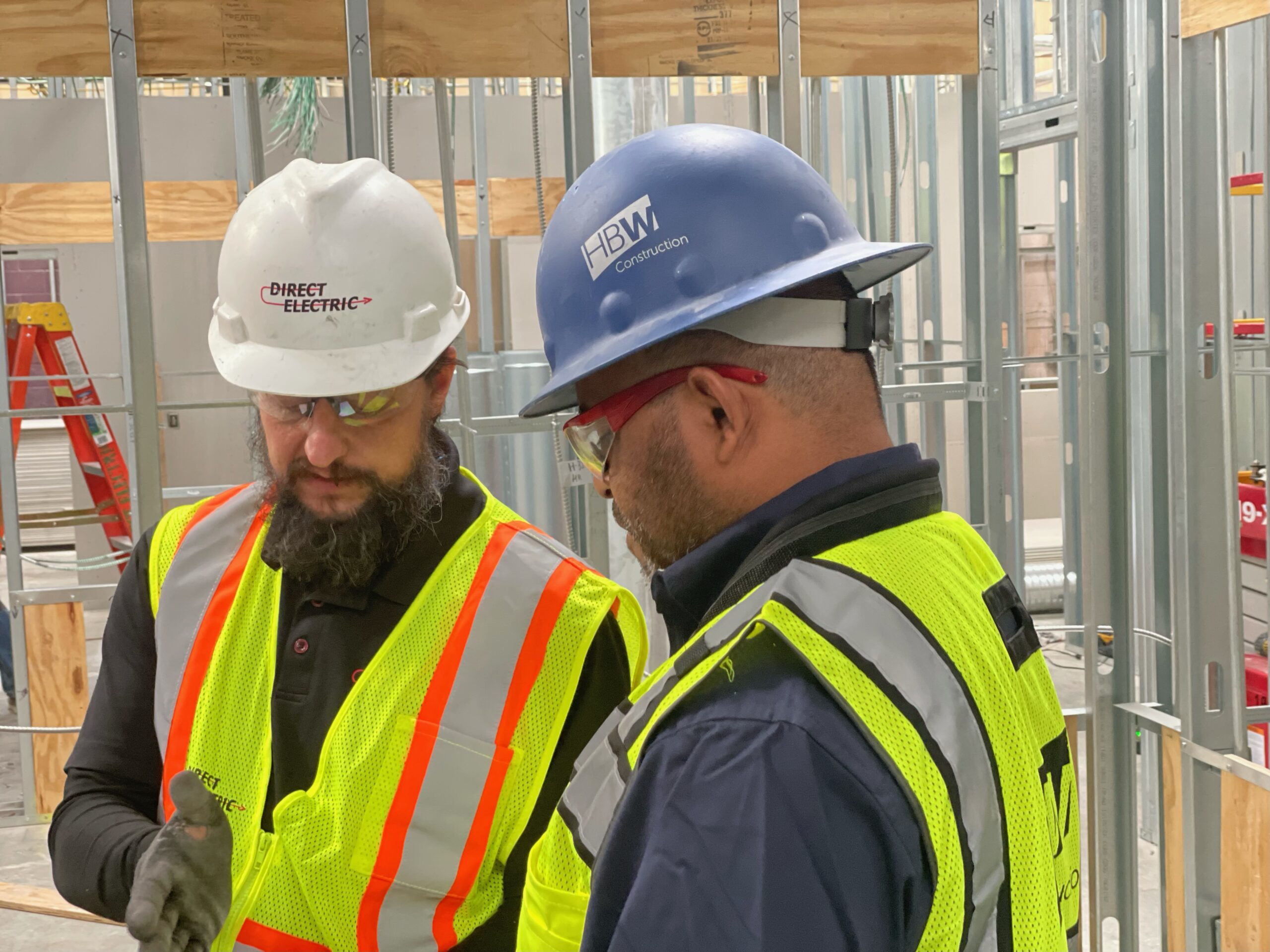
Big picture, small details
We’ve found that planning is key to safety. By thinking through the job, the people, the activities, and the risks, we can ensure everyone’s properly prepared to do their job. It is our way of gaining control over the 80 percent of safety risks that are the result of behaviors.
One challenge is that safety comes with infinite amounts of information. How do we know we’re handling every situation correctly? Following the latest regulations? Doing all that we can? HBW employs a safety consultant to supplement our own extensive knowledge of safety protocols and procedures.
The consultant helps us look at the big picture – driving a culture of safety – and drill down into the smallest details, including advising us on special safety processes for unique situations or new equipment. OSHA protocols can seem time-consuming and arduous, especially with tight construction schedules, so having a safety expert on hand keeps everyone focused on doing things right by doing them safely.
The construction industry is also constantly changing. As the industry learns new information, our training and the expertise of our safety consultants, help us apply it to our work before OSHA regulates it so our people have the best possible working conditions.
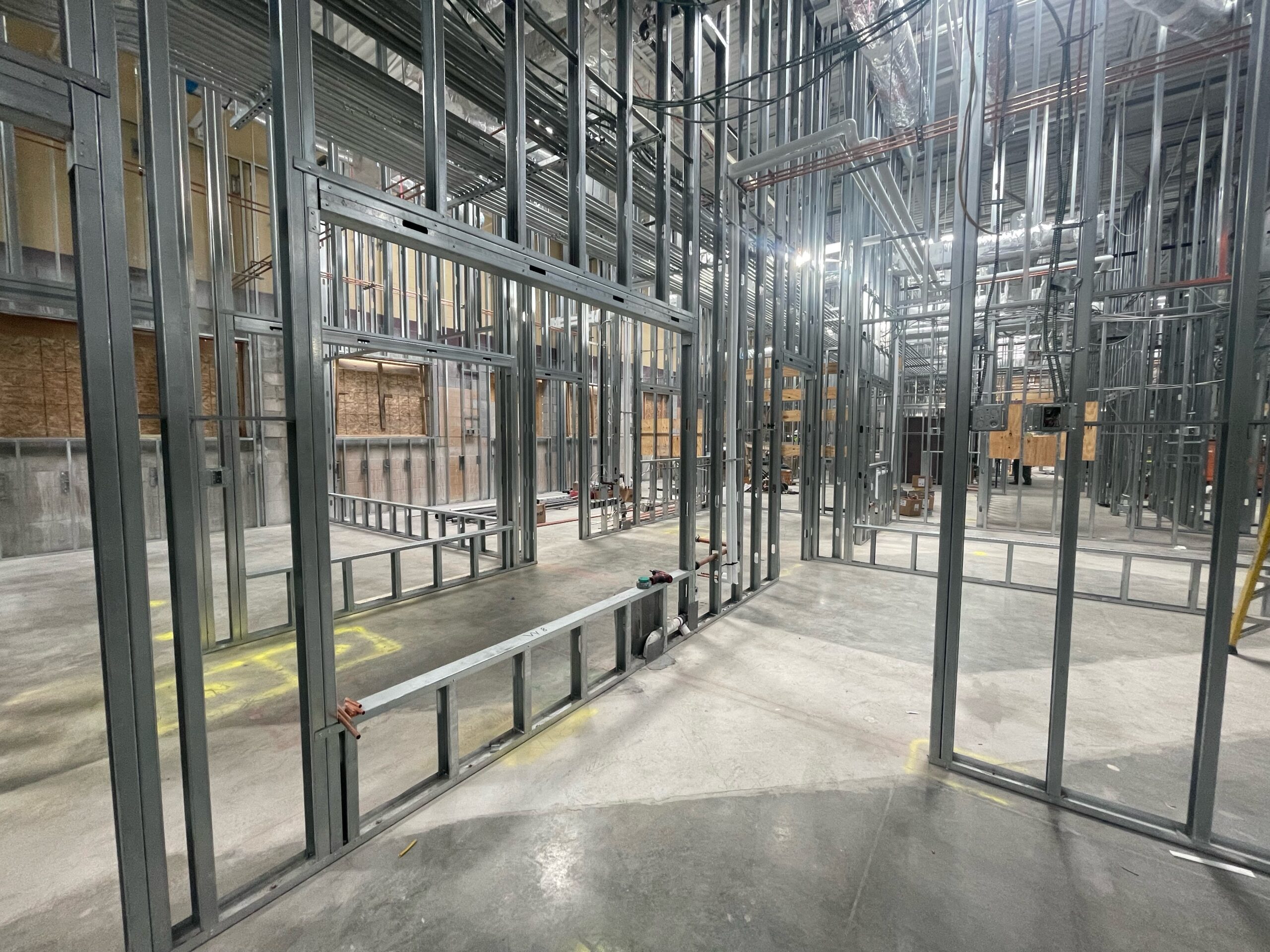
Trust but verify
Our safety consultants aren’t just there to advise, we also ask them to conduct mock OSHA inspections of our job sites – to verify that we are doing things correctly. These visits highlight any deficiencies so immediate action can be taken to improve.
Our Field Operations Coordinator schedules five safety visits to job sites each week. Jason Sears of Diversified Safety Services, a certified Construction Safety and Health Technician, walks the site with each Superintendent, using OSHA checklists and taking photos to help them recognize and mitigate safety issues. Jason’s keen eye catches problems in the making – so they can be addressed immediately and systemically – applying what we learn on one job site to all of our sites.
“HBW has a true dedication to safety that reflects how they feel about their employees, their subcontractors, and their clients,” says Jason. “Their work might not attract the attention of local state or federal compliance officers from OSHA because they don’t have a giant crane poking into the skyline, but internally they have the expectation that every part of the job will be done perfectly. Knowing our partnership helps them achieve that means a lot.”
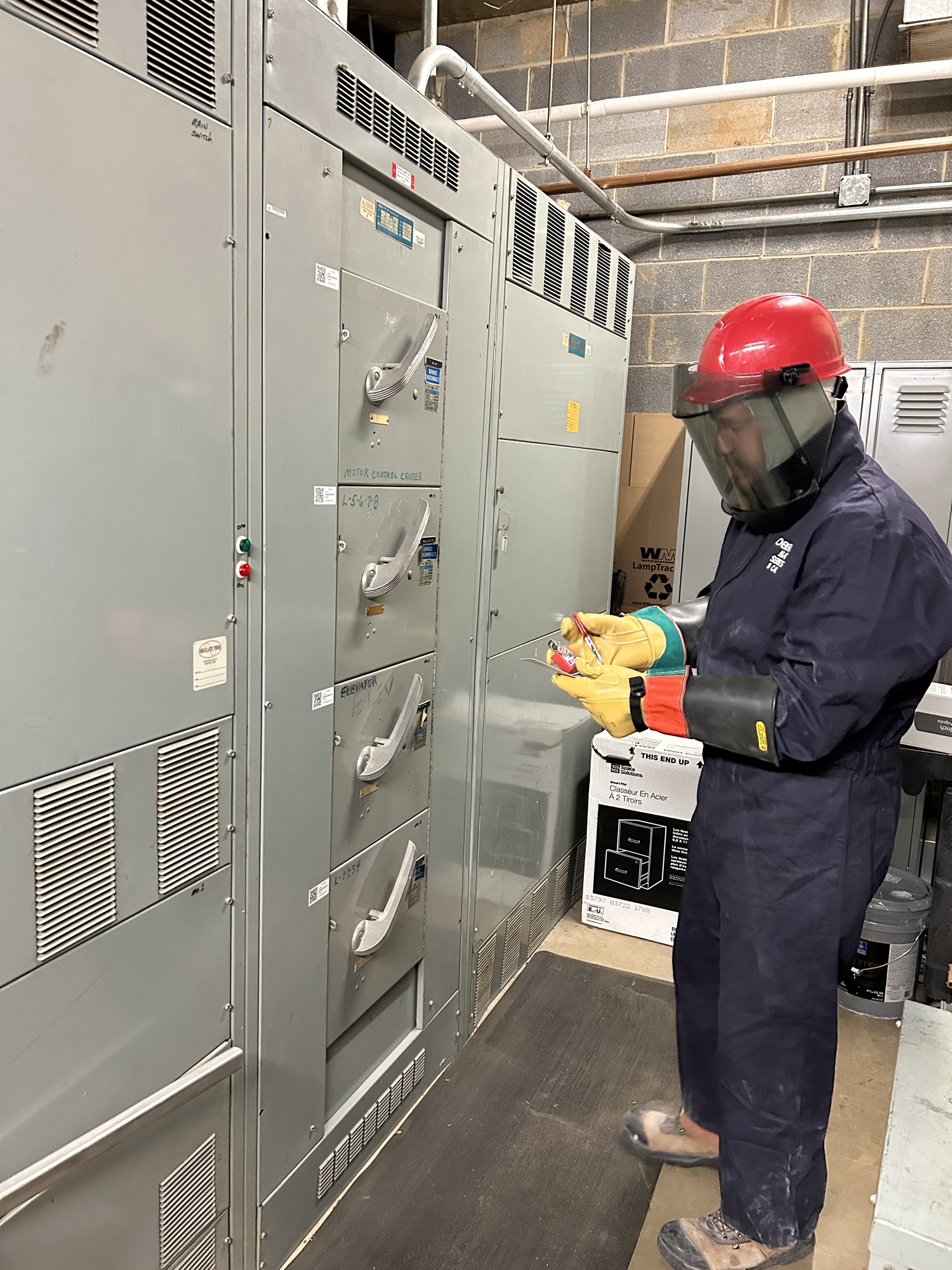
Right on time
HBW job sites have signage that states our safety guidelines, but we know that written words aren’t enough to keep everyone safe. That’s why our Superintendents conduct Toolbox Talks. These important meetings can be held daily, weekly, or spur of the moment. They gather everyone on the job site, have them sign in, and then go over our safety standards, spelling out how things should be handled on the site.
Reinforcing safety in the moment makes a difference. It leaves nothing to chance. If a supervisor has jackhammers in use, he or she may do a quick Toolbox Talk to discuss ear and eye protection for those doing the task – and those nearby. Plus, they can discuss how they will sequence work to keep everyone safe.
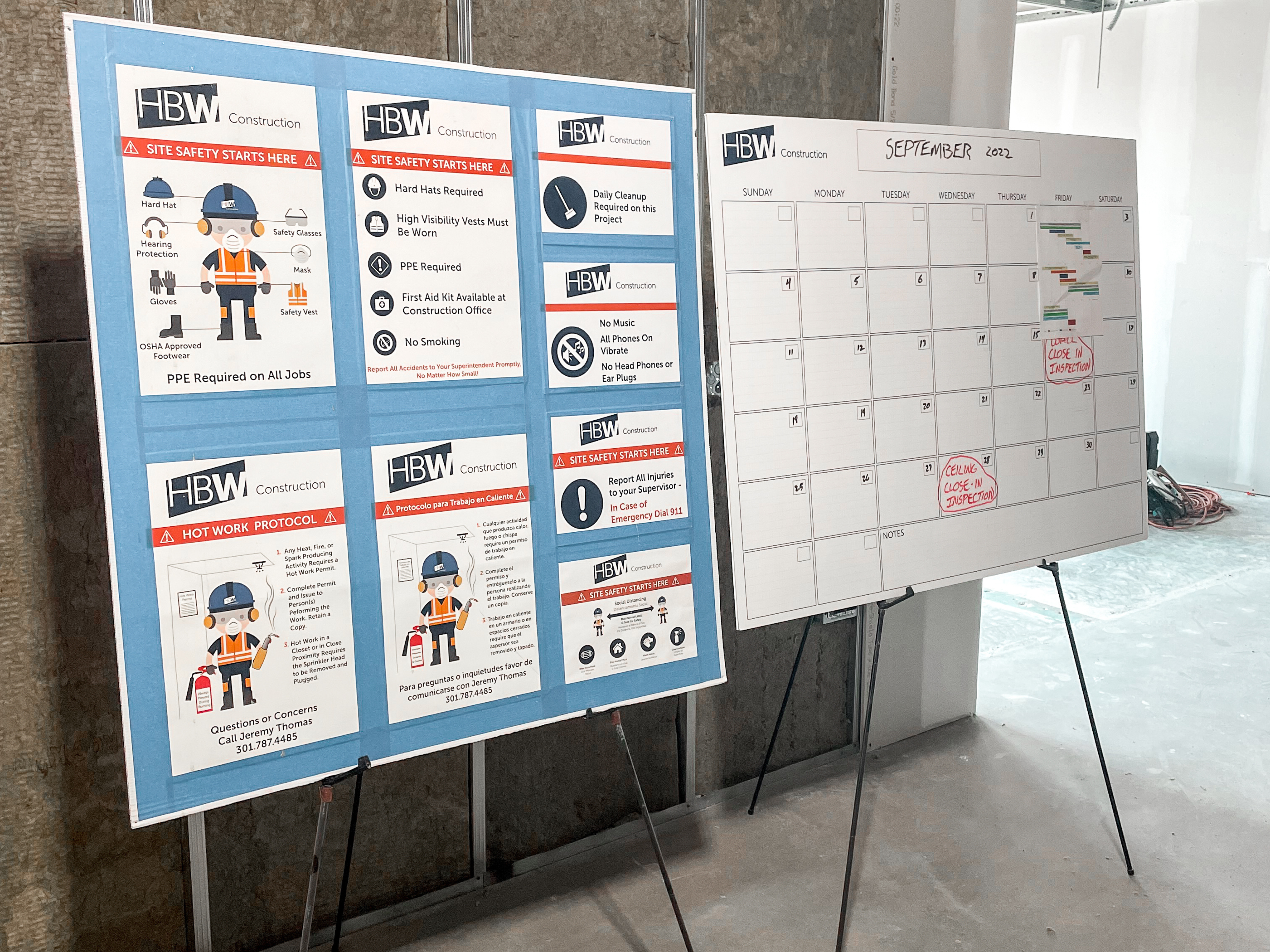
Industry involvement and leadership
HBW Construction has a long history of involvement with construction safety organizations and leadership in our industry. We are a part of the Maryland chapter of the Associated General Contractors of America’s (MDAGC) Safety Group. They are a resource for OSHA training courses, first aid certification instruction, and industry best practices. Our involvement is a clear sign to our subcontractors and our clients that we are dedicated to safety.
Significantly, the AGC recognizes safety efforts with awards, incentivizing general contractors to up their safety game and highlighting those companies with few or no accidents. HBW was recognized in 2016, 2017, 2018, 2019, 2020 and 2021 for the AGC Safety Excellence Award. This award is given to GCs with a combined incident rate below the Bureau of Labor Statistics average.
Quality goes hand in hand with safety – it’s how we get the job done during Construction Safety Week and every day.
Learn more about HBW’s quality control program on our website.
At HBW, we believe that learning never stops; an inquisitive mind and a willingness to learn are essential in an evolving and increasingly technical industry.
To help our colleagues better understand the processes for budgeting and scheduling, HBW Construction has developed two continuing education courses: Budgeting 101 and Scheduling 101. These courses are taught to architects, real-estate leasing brokers, construction managers, and others during construction lunch and learn sessions featuring HBW’s own experts.
Having courses that earn professional continuing education credits reflects the quality of our material and our instructors. Our coursework is accredited by the American Institute of Architects (AIA). Truthfully, we don’t know of any other contractor who teaches a class that earns continuing education credits.
Our team of experts work with budgeting and scheduling concepts and tools daily, which means that we are very up-to-date on costs, supply chain issues, design trends, and customer concerns, making our classes appealing and immediately useful.
Budgeting and Scheduling
Budgeting 101 teaches students the means, methods, and best practices used for quantity take-offs and unit pricing strategy. Gaining a better understanding of the construction budgeting process allows designers and others involved in planning to provide the details an estimator needs for a more complete and accurate budget.
We offer our construction budgeting course because we believe realistic budgets are a collaborative effort, whether you work with HBW or another company. The market has become very cost-conscious, and everyone involved wants to know – down to the penny – how much things are going to cost. Ballpark numbers leave too much room for error. HBW does 40-50 hard bids and 20-30 budgets a month, so we have a better idea than most of what design choices cost.
For our colleagues in leasing, having a realistic idea of what they can provide within the tenant improvement allowance (TI) impacts marketability, lease prices, and even tenant relationships. Our course can make the difference between a tenant moving into a space with expectations met and excitement or over-budget and disappointed.
As part of our construction budgeting course, we give students the tools they will need to understand and speak the language of an estimator to more accurately provide cost analyses to their clients for different build and finish requirements, including our own unit price comparison chart, project type comparison chart, and budget request form. We demonstrate how we build a budget based on real plans.
Scheduling 101 is taught by HBW’s scheduling pros – leveraging our experience to help future projects run smoothly. The course teaches the Critical Path Method of scheduling used in our operations. Like budgeting, construction scheduling helps set expectations with clients and our subcontractors far more effectively than looking at a calendar.
The construction scheduling course includes capturing all the steps in a build, how much time certain tasks will take, scheduling trades to do the work, and how long it will take to procure everything for the project. Because we’re familiar with what can go wrong during a build, we demonstrate how to be proactive and plan for things that might cause delays. We also explain the concept of floating, which allows some shifts in a schedule.
Our construction scheduling course uses a real example the students can relate to, starting with the due date and working backward. Students are taught to read a schedule, which is often more important than knowing how to build one themselves because it can help them understand a project’s status at a glance.
Enhance your knowledge with HBW Construction
For more than 50 years, our mission at HBW Construction has been to deliver highly personalized service and build trusted relationships. Offering budgeting and scheduling courses allows us to share our expertise with other industry professionals, helping them become better partners throughout the construction process. And that benefits the end-customer experience by accurately managing expectations for the cost and timing of construction.
To learn more or to schedule an HBW class, please email HBW’s Vice President, Patrick Foley pfoley@hbwconstruction.com.
At HBW, we are scheduling pros – leveraging our past experience to help every future project run smoothly. Our continued success is based on results, and that includes calendar management.
We use the Critical Path Method of scheduling in our operations. The critical path is determined based on activities and their duration, the sequence of activities, and the relationship between activities. Each activity directly impacts the completion date for the project. So, activities running a day late means the end date is impacted by the same number of days.
We think of it like setting up a domino course. We sketch out the big-picture vision of the schedule – what things need to get done to complete the project. That’s like laying out a course.
From there, we fill in the dominos – who needs to be there and on which days. We know that once a solid schedule is created, things cascade as each domino impacts the next, right down to the last one falling right on time.
Our scheduling and time management provides marching orders, but the key to making it all work is communication. We use day-to-day planning to set expectations with our clients and our subcontractors. The process doesn’t work if we are just showing them a calendar. What does work is having a dialog about the plan, with everyone involved providing feedback about how much time certain tasks will take or how long we need to allow to procure everything we will need.
The initial stages of scheduling are where experience makes all the difference. Often the projects that we’re doing aren’t really all that different from other projects we’ve done in the past. We know how long it takes to hang drywall, or install light fixtures, and we’re familiar with what can go wrong during a build. That knowledge allows us to be proactive and plan for things that might cause delays.
Let’s look at strategies for creating a schedule and helpful schedule tips.
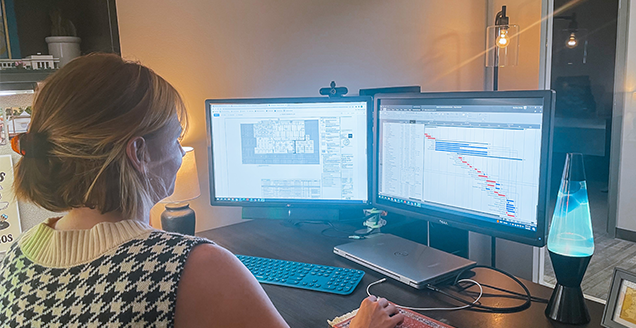
Start at the end
The end is a good place to start. We like to begin every schedule by asking about the timeline the client, the tenant, or the broker has in mind – and what’s driving those expectations. From there, we can work backward, roughing in design, procurement, and construction phases in the schedule to determine if that date is realistic and possible.
Of course, you want to hit that end date but it’s more important to set expectations for what is actually possible. Once you do, you can sweat the details and be on top of following up with suppliers and manufacturers to ensure there are no delays and no surprises.
Map out and list the activities that will be required to build the project
The next step is to list out all of the activities the project requires and their duration, pulling in my construction managers and trades to make this list as complete as possible
- Reviewing the project documents
- Reviewing building requirements
- Consulting with our construction managers or colleagues who have done similar projects in the past
- Consulting with trades performing the work
It’s helpful to categorize the activities based on the structure of the schedule.
Design: All activities necessary to produce a set of documents to communicate the work to those performing the work.
Procurement: Activities that involve gathering the materials that will be needed and lead times for materials that must be ordered or built.
Construction: Activities necessary to produce the work, often subdivided into steps required by each contractor.
Relationships/Links: Understanding the relationship between activities allows you to schedule activities in order, sequencing those dependent on other work, and listing successors and predecessors for each.
Milestones and Benchmarks: These are deliverables like Concept Drawings in the Design phase or Ceiling Close-in in Construction.
By placing activities in their sequence, you’ll have created an initial schedule.
Create and refine
Scheduling is an iterative process. As the project progresses, we’ll refine the schedule based on how long activities actually take.
We use a concept called float to understand the timing for each activity. Float is the number of days that the activity can be late before it impacts the completion date. For example, rough-in electrical boxes have a Float of 0. That means the activity must start on the identified start date and be completed within the identified durations. If the activity starts late, we must either reduce its duration to complete it on time, or its end date will push, affecting other activities. Float allows us to make decisions on individual activities by showing how each will impact the schedule.
What about contingencies?
Scheduling is a delicate balance between having enough time to get everything done, and shortening time on site to avoid burning through resources. Planning helps anticipate activities that have a bigger float and limits some of the risks involved in each project.
We frontload our schedules, working ahead whenever possible so if something unexpected does crop up, we have options. For example, if light fixtures are delayed, and we have “float” in the schedule, we can consider our options: wait on installation, replace those fixtures with another product that is available, or install temporary fixtures until the new ones come in. Frontloading helps us be more proactive and less reactive, just like planning a project schedule in the first place.
Become a Scheduling Pro With The Help of HBW Construction
Benjamin Franklin didn’t work in construction, but he recognized the importance of time management for successful outcomes. We are proud to call ourselves scheduling experts. If you’re interested in learning more, HBW offers a Scheduling 101 course for continuing professional education credit. To learn more, visit, https://hbwconstruction.com.
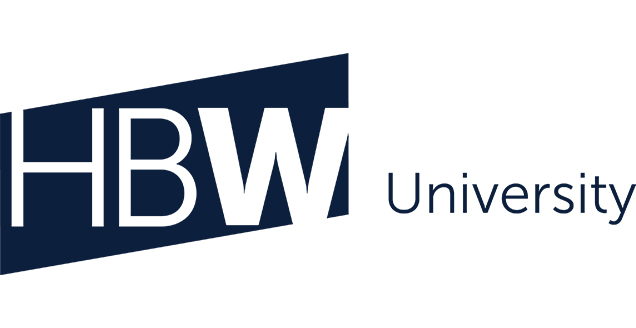
Over several years of transforming the construction project schedule to be focused on the client, HBW Construction has gained strong buy-in from general contractors, subcontractors and clients for a zero punch list process. There are many important advantages to this process, including:
- A focus on quality work throughout the project
- Happier clients on the final walk-through
- Timely project turnover
- Less time and money spent on crew return visits
- More profitable projects
Zero Punch List Process
The phrase “punch list” comes from the antiquated process of punching holes in a list to mark items that need fixing. The modern punch list includes items that do not conform to contract specifications or items that were damaged during the construction process. It can also include items that were incorrectly installed or not functioning as promised.
Historically, the client or project owner had significant responsibility for identifying punch list items and communicating them to the general contractor. The general contractor then communicated punch list items to project partners and subcontractors, who then scheduled any needed crews to fix and check off the items. This all happened toward the end of a project.
If quality control was handled well throughout the project, punch lists only included small fixes the client identified during the final punch list walk-through. But over time a punch list became a catch-all for all kinds of project problems, leading to construction project schedule delays, extra expense and unhappy clients.
Alternatively, a zero punch list process anticipates any final fixes and takes that burden off the client. Our aim is to surpass client expectations during the final walk-through and reveal our best work.
How do we achieve the zero punch list? First, we hold weekly project meetings to address scheduling progress, workmanship, missing materials or clean-up issues. These weekly meetings occur throughout the project with subcontractors and the client. We are on site with the client, or we do weekly virtual walk-throughs and progress reports by video. Any issues identified during these weekly progress meetings are fixed on the spot.
If we are experiencing supply chain issues, we try to anticipate delays and work them into the project schedule or suggest alternative materials to keep the project moving forward with all items in place. Our goal is to avoid delays in key materials that would prevent us from turning over the project to the client on time.
As the project nears completion, we schedule our final client walk-through. A unique aspect of our zero punch list is that subcontractors have crew members on site for the final client walk-through. This has become standard on projects that we manage.
Before the client arrives for the walk-through, we take out our blue tape. We walk the project ourselves and note any final paint or trim touch-ups and address any final clean-up needs.
Exceeding Client Expectations
When the client arrives, blue tape is evidence of minor scratches or dings we have already identified. Crews on site will follow behind us and fix these items the same day of the walk-through.
Our zero punch list walk-through is transformed into a reveal party. We highlight design features. We let the client test the lighting and try out the appliances. If we followed our process well, we should only hear positive comments and excitement from the client about moving into the new space.
When our entire project team is focused on attention to detail and quality, the client is not left responsible for pointing out sawdust, loose screws or paint dings. We want to avoid the expense of punch list work beyond the original construction project schedule. Most importantly, we want to create long-term client satisfaction.
The zero punch list not only keeps clients happy on a single project, it also often results in repeat work. Through our weekly project walk-throughs and communications, our subcontractor collaboration and our trusty blue tape, we offer a new standard for construction quality.
Electrical shutdowns can be handled efficiently as part of commercial construction services if the project team plans for them. At HBW, we follow a consistent electrical shutdown safety process in accordance with OSHA and other safety standards. In fact, our clients and many of our partnering GCs and subs have adopted this standard. Together with our trained supers and field crews, we are helping to raise the bar on construction safety.
Protect your crew and the construction project schedule by planning your electrical shutdowns. Here are some takeaways from the HBW Construction process.
1. Anticipate electrical shutdowns in the schedule.
One of the best ways to integrate safety with the construction project schedule is to plan for electrical shutdowns during the initial stages of the project. Make it part of your project management. You could also add a safety consultant to your planning and oversight.
Not every project requires third-party safety oversight, but a consultant can verify your crew’s readiness for a shutdown long before it happens.
“Coming up through the construction industry, I’ve seen that a schedule delay is only the tip of the iceberg if your project experiences a site injury or fatality,” said Jason Sears, CHST, a field operations manager with Diversified Safety Services in Maryland. “It affects crew morale, job security and the continued operations of the company. There is a trickle-down effect on all aspects of the business beyond one incident.”
As part of HBW’s process, we require a 7-day notification prior to an electrical shutdown. Our electrical subs complete a de-energize permit and walk through our lockout/tagout checklist. We developed the permit in cooperation with Diversified Safety Services.
2. Communicate 48 hours before shutdown.
With your project management plan in place, develop a communications protocol for 48 hours before the planned electrical shutdown. With all the key players in attendance, use this meeting to walk through the shutdown process and who will be responsible for tagouts and other steps.
For efficiency, this meeting can be done virtually with a superintendent and/or safety consultant on site. We developed this process during the pandemic and have kept it as an option for geographically distant projects.
If your project is occupied or requires communication to building management, develop a consistent message for the timing and length of the shutdown. Allow for a 48-hour advance warning to tenants or the public. If you can let the client know sooner, all the better!
3. Invest in and use proper PPE.
Make sure that the electricians and anyone working around live energy is protected with an arc flash suit, gloves, a face shield or helmet and electrical safety shoes such as leather shoes with protective toe boxes.
We have seen inconsistency in PPE ratings on job sites. Our crews are required to have the best rated PPE on site for electrical shutdowns and other hazardous activities.
4. Test your testing equipment.
Testing equipment should be onsite and in proper condition to test for zero voltage prior to conducting work. Equipment should be properly insulated. Before shutdown, the meter should be tested on a safe outlet to make sure it’s reading the proper voltage.
Lots of eventualities can happen with electrical shutdowns and a zero- voltage policy will remind crews to test circuits and confirm that the system is de-energized.
Testing may also identify if existing panels have had a tighten-up (regular maintenance); this will manage crew risk with loose connections on breakers or lugs. Older switch gear should also be properly tagged as part of the shutdown.
5. Use a lockout/tagout checklist.
On the day of the electrical shutdown, follow the lockout/tagout protocol discussed during your planning meeting. Your superintendents can be the checks and balances to take the right approach and maintain crew safety.
With this approach, we have seen at least a 50% increase in superintendents who are taking the initiative and planning for electrical shutdowns. Planning helps them maintain the construction project schedule, but also builds trust with the crew.
Capable and healthy construction crews are critical to company success. Ask about our electrical shutdown logout/tagout kit and safety procedures for your future project.
[rl_gallery id=”8000″]
Resources:
OSHA Standards and Resources –
Diversified Safety Services – Field Operations Manager Jason Sears, CHST, contributed to this article.
Without this early collaboration, projects can encounter costly change orders and delays in the construction project schedule. Even with collaborative project partners, industry standards for layouts don’t always account for the physical realities of a three-dimensional space.
With this in mind, HBW developed a more extensive layout process that essentially organizes each element of the project by color. We take extra time to plan the layout, and then our crews snap color-coded chalk lines on site to reveal a physical matrix of all the trades. This layout helps us to identify constructability issues within days of project start, and it also supports an understanding of design intent.
Supporting Design Intent and Alternate Solutions
A classic challenge for constructability is ceiling height. Modern designs favor high or exposed ceilings, and this leaves less space to integrate plumbing, electricity, HVAC, or other infrastructure within the ceiling cavity.
By laying out the various trades by color, we can balance the design intent for light fixtures or ceiling finishes with the layout of elements such as sprinkler systems and existing ductwork. This also allows HBW to review service access to all equipment on day one with the building’s engineering team, rather than waiting until the end of a project.
A more detailed layout also smooths the process for helping clients choose alternate lighting, flooring, furniture placement / ordering of furniture or appliances much earlier in the project when necessary. The design team can help the client visualize the realities of the built environment before we build it.
The details in our layout have helped vendors select and order products earlier, giving them breathing room for longer lead times on manufacturing and shipping. If we can demonstrate the final dimensions of windows before they are installed, vendors can measure and order custom window treatments earlier in the project timeline.
Trend-Setting Layout Process Adopted by Project Partners
After experiencing the benefits of HBW’s layout process for the construction project schedule (due to a more seamless flow between trades and fewer change orders), some of our architectural partners now require this layout as part of their approach on every project. Ultimately, taking extra time on the layout protects project partners — and the owner — from project delays. It does not delay project start, but it helps them avoid more expensive re-design or re-engineering in the future.
The layout process also helps superintendents. Training is relatively easy for new crew members, and we find that it supports strong subcontractor relationships. It requires less reference to plans because they are literally color-coded in the construction zone itself. Superintendents can also refer to the layout while walking the construction site because the project is reflected on the floor. This also helps the superintendents re-direct the sequencing of the project due to material lead-time issues. And when there are constructability challenges, our crews can devise solutions faster and bring better ideas to the architects and engineers.
When the general contractor, architects and engineers have more time and space to identify constructability conflicts before construction, everyone is happier and able to perform at their best.
[rl_gallery id=”7709″]
Learn more about HBW’s job site management.
In addition to CDC guidelines, OSHA requirements and other standards, we perform an Infection Control Risk Assessment (ICRA) as part of our construction planning process. ICRA is a systematic process that determines the effects of construction or renovation activities on air or water quality, assessing the level of risk to patients, visitors or staff and defining controls to reduce that risk.
Now, new guidelines known as ICRA 2.0 are helping project teams better assess, prepare and manage identified risks. The ICRA 2.0 matrix is published by the American Society for Health Care Engineering (ASHE) and other professional groups and associations in cooperation with the Centers for Disease Control and Prevention.
A multi-disciplinary team of infection prevention and control, industrial hygiene, construction, facility management specialists and other authorities worked together to develop ICRA 2.0.
The ICRA 2.0 matrix provides even greater clarity for hospital design and construction, but we think these precautions are applicable to any project for infection risk control. Tenant-occupied projects are one example, especially those that involve vulnerable populations such as the elderly.
[rl_gallery id=”7655″]
How is ICRA 2.0 Applied in Construction?
During project planning, we will discuss how to assess and apply ICRA precautions to the project. This often involves setting up a sealed perimeter around the construction area with temporary walls and plastic, which allows us to create a sealed, negative air pressure environment. Air cannot escape, and it is in turn drawn into the construction area by way of an air scrubber that has dual HEPA filters that capture dust and particulates. The air pressure is monitored to maintain a consistent, negative air pressure environment (Digital Room Air Pressure Monitoring System with Alarm).
Project by project, we can apply ICRA precautions for removal, construction or inspections involving:
- Ceilings
- Fan start-ups/shutdowns
- Flooring and casework
- Drywall
- HVAC, electrical or fire suppression systems
- Plumbing systems
Any carpentry work that involves sanding, painting or significant vibration/noise is taken into consideration for minimizing risk to patient areas. This includes areas with high-risk patients who are immunocompromised or undergoing invasive treatments. ICRA 2.0 also designates medium risk areas, such as waiting rooms, a cafeteria or a gift shop.
Other Quality Control in Construction Safety Measures
Whether we are working on a hospital or another project, we consider the health and safety of the public, client staff and our HBW teams.
This includes how we remove debris from construction sites. We can cover containers that include debris, and we can lay down sticky mats to capture debris from shoes or carts going in and out of the construction areas.
If there is a chance of finding hazardous materials, we alert the client and call in special mitigation teams for its careful removal.
We provide our crew members with personal protective equipment such as high-grade masks, goggles and gloves.
If additional job site precautions are needed or requested, we factor them into the construction project schedule (and manage them through ongoing communication) to help the team meet client expectations for completion.
We want to be part of the solution from day one. If you have any questions about infection risk control for your upcoming project, contact us.
Learn more about HBW’s quality control and safety practices.
Prior to the pandemic, we could proceed with submittals and approvals with confidence that materials would arrive within their normal timelines. We created schedules for the construction team with built-in permitting and inspection dates. In multiple jurisdictions, we moved projects forward with relative ease toward completion.
New Realities of Construction Project Management
Successful commercial construction management demands experienced project managers (PMs) to navigate material submittals and approvals as well as timely permitting, sub-contractor scheduling and inspections. PMs must be on guard for anything that might cause delays, increase costs or impact quality. They need to identify and pursue alternative solutions as necessary.
Since the start of COVID, that experience was put to the test.
The uncertainty of materials delivery dates has essentially upended the construction project schedule. PMs can’t count on mechanical components or lighting packages to arrive when they used to. Common items like kitchen appliances, insulation or carpeting get back-ordered or quickly go out of stock. Delivery timelines shift based on a product’s country of origin or delays by manufacturer, distribution or shipping.
We have also experienced delays in permitting and inspections across jurisdictions due to Government office shutdowns, remote staff or limited staffing.
Despite these disruptions, your project can still happen. It requires agile and experienced project managers who know how to communicate, do their research, plan ahead and adjust to constant change.
The New Construction Project Schedule
Since the pandemic, communication and follow-up are more important than ever. Our approach begins with the materials list to determine when we can expect materials to be on site, and then we work backwards from those expected delivery dates. We also build in a buffer to account for unexpected delivery delays.
If we track shortages among certain products, we may order them immediately and store them until we need them on site. We have also taken steps to lock in prices on materials in short supply.
Planning and communication don’t end there. Our PMs are in constant communication with manufacturers, distributors and suppliers to confirm deliveries. If a significant delay is detected, we will circle back to the design team and client to see if substitutions or alternative materials will meet project specifications. If alternative materials are approved, then the design team will check and reconfigure as necessary to fit that alternative.
Project start dates and construction phases are aligned with permitting and materials deliveries. Once work begins on the job site, we want to keep crews on site making progress. Certain phases of a project that normally happen early may get scheduled in a later phase to coincide with materials delivery. As each phase is complete, we anticipate and communicate to schedule timely inspections.
Needless to say, weekly progress meetings are full of updates about scheduling, deliveries and any uncertainties that need follow-up.
Tips for Your Project
Pandemic-related supply chain issues are a reality that continue to impact current and planned construction projects. An experienced commercial construction management team adapts to these variables and uncertainties. The best teams are leveraging their supply chain connections and technology to update project data in real time. Frequent updates support client confidence and peace of mind.
You can rely on this approach at HBW. We have adapted our services to manage constant change in the supply chain and in the field. Call us to talk about your upcoming project.
Learn more about HBW’s experienced project management services.
Some changes, such as videoconferencing capabilities, have improved communication clarity and efficiency throughout a project. On the safety side, our efforts with masking, temperature checks, social distancing and contact tracing reduce illness and absenteeism.
What should clients and project partners expect from their construction team going forward? We anticipate continued use of safety best practices that we’ve learned from our job sites in a pandemic. When you choose a commercial construction firm, consider these practices as part of overall quality control in construction.
Communication Expectations
Going forward, project partners will need to move fluidly between hybrid and remote communications. This means that superintendents should have the most up-to-date videoconferencing platforms available to them — as well as training on those platforms to set up or attend meetings.
We learned in 2020 that each jurisdiction may also have different regulations with regard to job site communications. In some cases, an inspector might leave the job site if a crew member was not masked or if the job site wasn’t cleared of crew upon arrival. We updated our field operations portal regularly to give our supers the most up-to-date information for 16 different jurisdictions. Staying informed on CDC, OSHA and other regulatory updates will continue to inform our safety protocols.
Improved meeting attendance is another positive outcome of accessible communications tools. Crews don’t have to leave the job site to hop on a video conference. Daily and weekly meetings are more efficient, and crew members can get direct and consistent updates. Ultimately, this approach enhances quality control in construction.
Crew Safety Expectations
Job site safety has always been a priority, but job sites in a pandemic have taught us the value of masking, social distancing, hand washing and clear signage more than ever before.
We quickly developed new bilingual signage for general pandemic protocols, but also for specific needs on job sites. For example, certain areas of job sites were closed off. Later, some job sites required masking while others allowed crews to work without mandated masks. In response, we created a COVID toolkit and provided training on its consistent use by each team member.
We have experienced the benefits of adapting protective gear for each job site. Pollutants like dust and silica are still present, and masking is already recommended for maintaining crew health. In addition to continued use of temperature checks and contact tracing through a subcontractor sign-in sheet, we have invested in anti-fog glasses, goggles and face shields.
After seeing the benefits of these changes on the job site in a pandemic, we have noticed that clients gravitate toward this level of quality control in construction. Proper job site management — as well as our Quality Control Program — help us to keep crews healthy. This supports our project goal of timely completion with a “zero punch list!”
Learn more about HBW’s quality control and safety practices.